Automatic CNC welding machine is a kind of welding equipment, which is mainly composed of welding device, control system, mobile device, etc., and can realize automatic or semi-automatic welding. It can automatically complete the welding process according to the set program or the operator’s instructions without human intervention. Automatic welding machine is mainly used in industrial production, which can improve production efficiency, reduce labor costs and ensure welding quality.
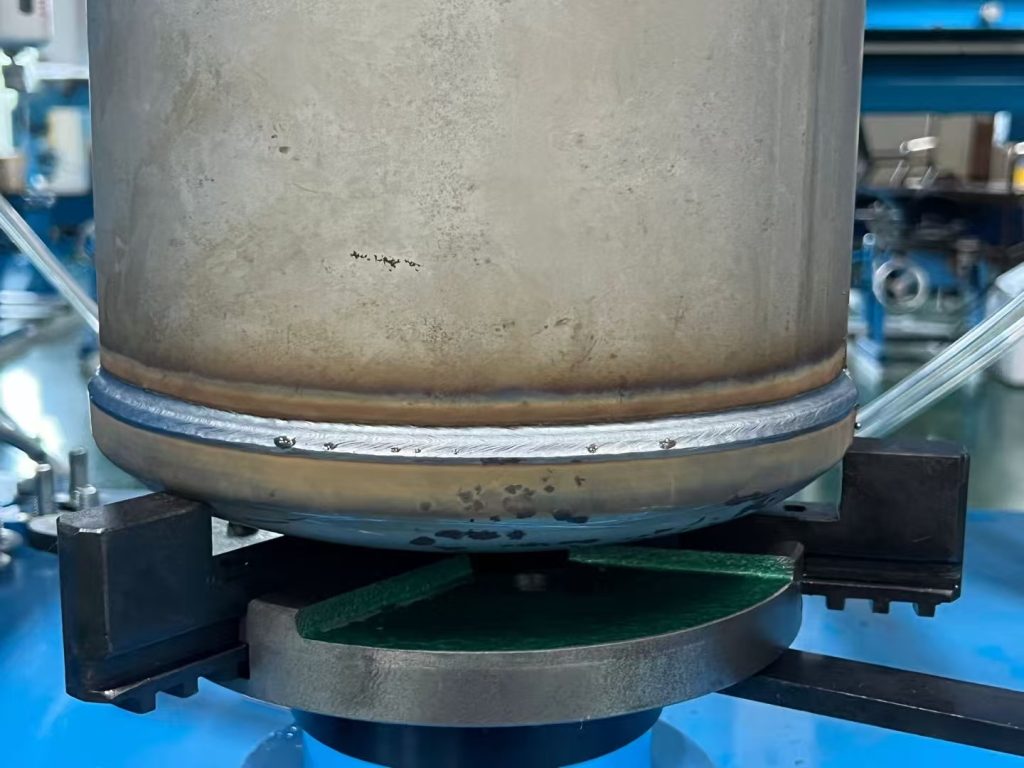
There are many types of automatic welding machines, including gas shielded welding machine, laser welding machine, electron beam welding machine, etc. Among them, gas shielded welding machine is the most commonly used one, which uses gas to protect the welding area, reduce oxidation and burning during welding, and improve welding quality and efficiency.
The advantages of automatic CNC welding machines include:
1. Improve production efficiency. Automatic welding machines can perform welding continuously, reducing the pause and waiting time of manual operation and improving production efficiency.
2. Reduce labor costs. Automatic welding machines can replace manual welding, reduce the number of welding workers and reduce labor costs.
3. Ensure welding quality. Automatic welding machines can perform welding according to preset parameters, avoiding the influence of human factors on welding quality and ensuring the stability and consistency of welding quality.
4. Improve welding process level. Automatic welding machines can complete some difficult and high-demand welding, improving the welding process level.
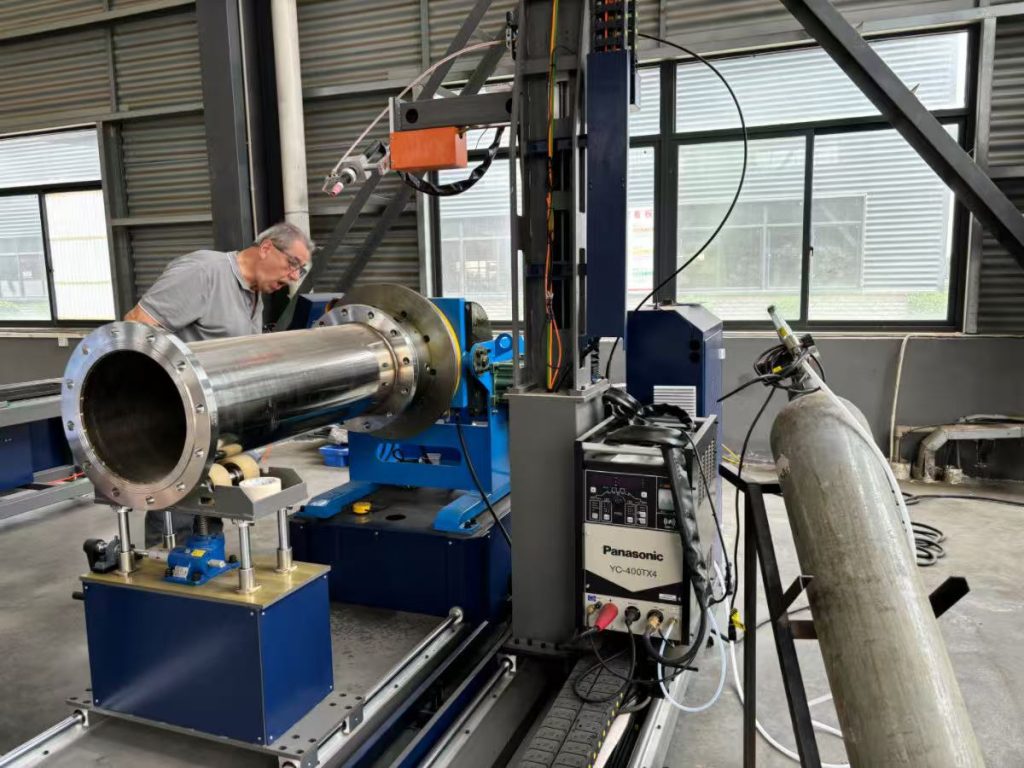
The use of automatic CNC welding machine includes:
1. Select the appropriate type and specification of automatic welding machine according to welding requirements.
2. Install and debug the equipment according to the instructions.
3. Set welding parameters, including welding current, welding voltage, welding speed, etc.
4. Place the workpiece to be welded on the welding device and start the automatic welding machine.
5. Monitor the welding process and adjust the welding parameters according to the actual situation.
6. After welding is completed, turn off the automatic welding machine and clean the workpiece.
It should be noted that the use of automatic welding machines requires certain skills and experience, and operators need professional training to master the correct use methods. In addition, pay attention to safety during use to avoid accidents.
In short, automatic welding machines are an efficient welding equipment that is widely used in industrial production. It can improve production efficiency, reduce labor costs, and ensure welding quality. It is one of the indispensable equipment in industrial production.
The speed of a CNC welding machine refers to the length or area of welding completed per unit time. Speed is an important indicator of CNC welding machine, which directly affects welding efficiency and product quality. The following is an introduction to the speed of CNC welding machine:
1. Definition and influencing factors of welding speed
The speed of a CNC welding machine refers to the length or area of welding completed per unit time. The welding speed is affected by many factors, such as welding current, welding voltage, welding heat input, etc. Welding speed that is too fast or too slow will affect the welding quality, so it is necessary to make reasonable adjustments during the welding process.
2. Classification of welding speed
According to the different welding speeds, CNC welding machines can be divided into low-speed welding machines and high-frequency welding machines.
1. Low-speed welding machine
A low-speed welding machine refers to a CNC welding machine with a welding speed lower than 30cmmin during the welding process. The advantage of this welding machine is that the welding quality is stable and it is suitable for welding thick plates, large structural parts, etc. The disadvantage is that the welding speed is slow and the production efficiency is relatively low.
2. High-frequency welding machine
A high-frequency welding machine refers to a CNC welding machine with a welding speed higher than 30cmmin during the welding process. The advantages of this type of welding machine are fast welding speed and high production efficiency, and it is suitable for welding thin plates, small structural parts, etc. The disadvantage is that the welding quality is relatively unstable, and some special process measures are required to ensure the welding quality.
3. Control method of welding speed
The welding speed of CNC welding machine can be controlled by programming. When programming, the welding speed can be set as needed, and the moving speed of the welding gun can be controlled by the CNC system. At the same time, it can also be adjusted in real time according to the actual situation to meet the welding needs of different workpieces.
4. The impact of welding speed on product quality
Welding speed that is too fast or too slow will affect the welding quality. If the welding speed is too fast, it may cause problems such as insufficient penetration and incomplete weld; if the welding speed is too slow, it may cause problems such as excessive penetration, too high weld, and weld nodules. Therefore, it is necessary to select the appropriate welding speed according to the actual situation to ensure welding quality and product performance.
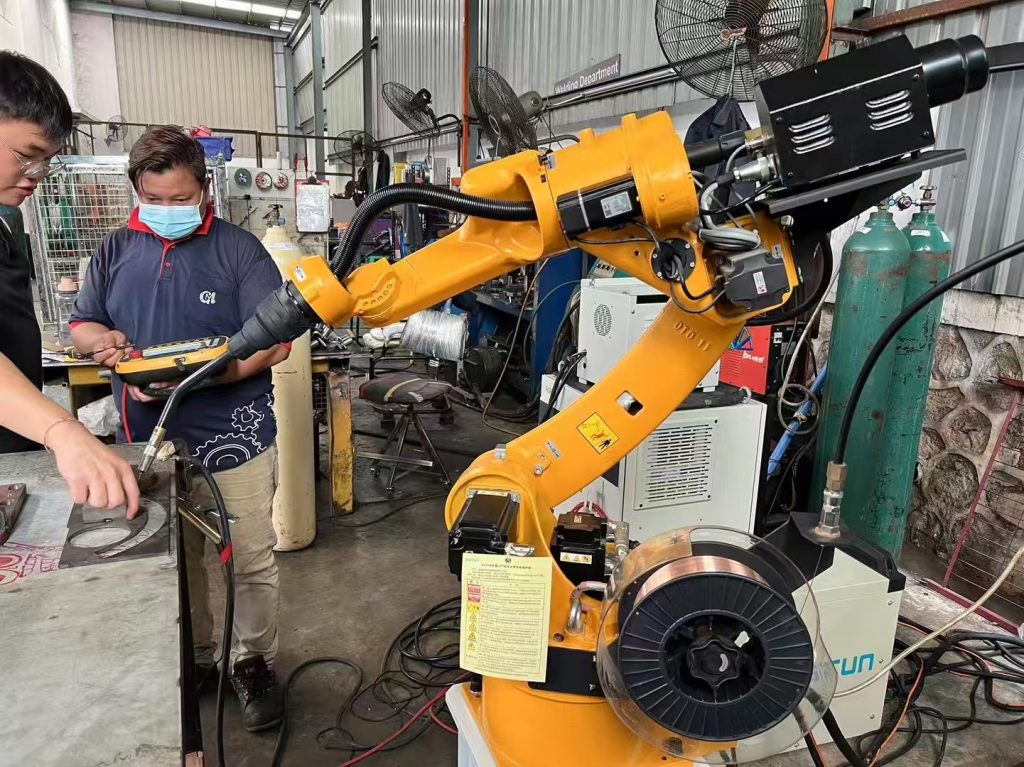
CNC welding machine solution
With the continuous advancement of industrial modernization, CNC welding machines are playing an increasingly important role in modern manufacturing. CNC welding machines have the advantages of high efficiency, precision, and automation, and are suitable for large-scale, high-precision, and complex structure production and processing. However, in actual application, CNC welding machines still have some problems, such as unstable welding quality, low welding efficiency, and difficult equipment maintenance. In order to solve these problems, we need to develop a comprehensive CNC welding machine solution.
The goal of this solution is to improve the welding quality and efficiency of CNC welding machines, reduce equipment maintenance costs, and thus improve the production efficiency and economic benefits of enterprises. To achieve this goal, we will follow the following principles:
Automation and intelligence: By introducing advanced automation and intelligent technologies, reduce human operation errors and improve welding quality and efficiency.
Reliability and stability: Use high-quality hardware equipment and optimized software algorithms to ensure the reliability and stability of the equipment.
Ease of use and maintainability: Simplify the operation process, reduce the skill requirements for operators, and facilitate equipment maintenance and maintenance.
This solution mainly includes the following aspects:
Hardware configuration optimization: Select high-performance CNC systems, power supplies, welding guns and other core components to ensure the basic performance of the equipment.
Welding process optimization: Through experiments and simulations, optimize welding process parameters to improve welding quality and efficiency.
Intelligent control: Introduce machine learning, deep learning and other technologies to achieve intelligent control of the welding process and improve welding quality and efficiency.
Remote monitoring and maintenance: Through the Internet of Things technology, remote monitoring and maintenance of equipment can be achieved to reduce maintenance costs.
Operation training: Systematically train operators to improve their skills and ensure the effective use of equipment.
How to choose high-quality CNC welding machine
Choosing a high-quality CNC welding machine can help improve production efficiency and quality, reduce failure rate and maintenance costs. Here are some key factors and steps to choose a CNC welding machine:
1. Clarify needs and budget
Before choosing a CNC welding machine, you need to clarify production needs and budget. Consider factors such as the type, material, size and output of the workpiece to be welded, as well as the price range that can be afforded within the budget.
2. Research brands and models on the market
It is very important to understand the brands and models on the market. Through channels such as the Internet and industry exhibitions, you can understand the performance, price, after-sales service and other aspects of CNC welding machines of different brands and models.
3. Consider key performance indicators
The following key performance indicators need to be considered when choosing a CNC welding machine:
Welding speed: Welding speed is an important indicator of CNC welding machines, which determines welding efficiency and product quality. Choosing a CNC welding machine with adjustable welding speed can meet the welding needs of different workpieces.
Power output: The power output of the CNC welding machine is also an important indicator. Choosing a power output range that suits your needs can ensure the stability and quality of welding.
Precision: The precision of the CNC welding machine is crucial to the production of high-quality products. Choosing a high-precision CNC welding machine can reduce errors and improve product quality.
Reliability: Choosing a CNC welding machine with high reliability can reduce the failure rate and improve production efficiency.
Operation interface: Choosing a CNC welding machine with a friendly operation interface and easy operation can improve work efficiency.
4. Consider after-sales service
When choosing a CNC welding machine, you need to consider the quality and scope of after-sales service. Understanding the brand’s after-sales service policy, technical support, spare parts supply, etc. can help solve problems that arise during use and improve production efficiency.
5. Conduct on-site testing
When choosing a CNC welding machine, it is recommended to conduct on-site testing. On-site testing can evaluate the performance, accuracy and reliability of the CNC welding machine, and can also understand the convenience and ease of use of the operating interface.
6. Consider long-term costs
When choosing a CNC welding machine, you need to consider not only the purchase cost, but also the long-term use cost. Including cost factors such as maintenance, spare parts, and power consumption. Choosing a high-efficiency, low-energy CNC welding machine can help reduce long-term costs.
7. Summary
When choosing a high-quality CNC welding machine, you need to conduct a comprehensive market research and evaluation. Consider factors such as demand, budget, performance indicators, after-sales service, on-site testing, and long-term costs, and finally choose a CNC welding machine that suits you.
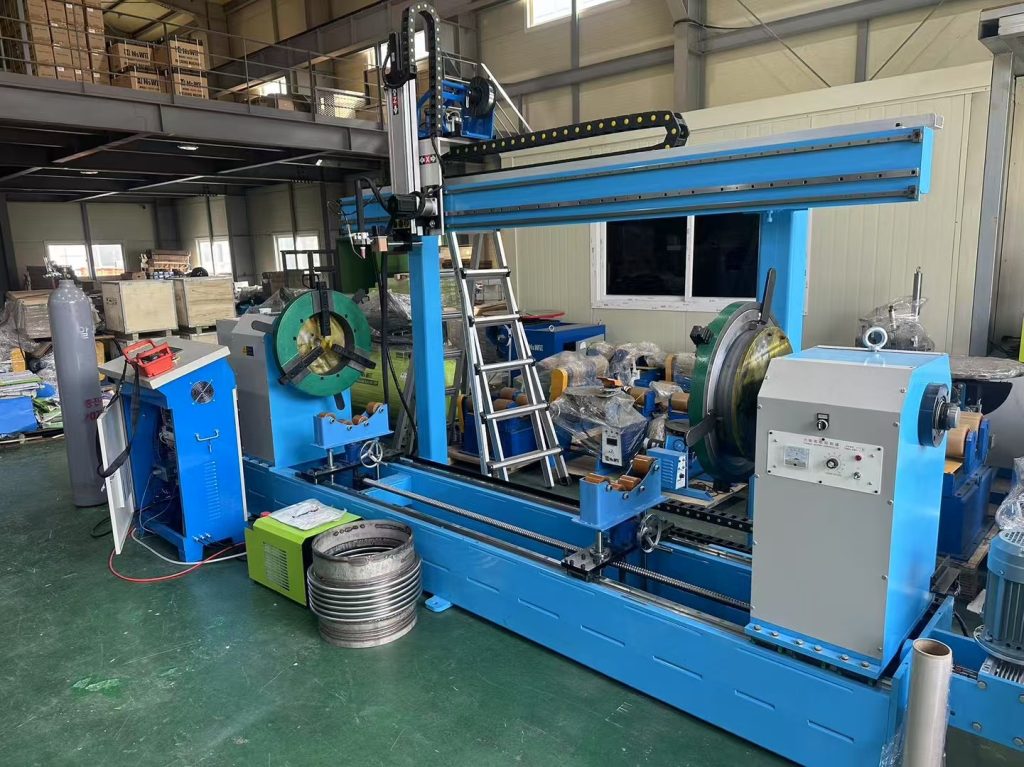